The DIY PRP system relies on a bench-top processing station for optimal collection of platelet-rich plasma (PRP). As the syringe plungers used in the DIY PRP system are trimmed and modified to fit inside a centrifuge for spinning, a processing station was designed in order to facilitate the manipulation of the plunger’s rubber stopper. The entire device is designed around a vertically rising rack and pinion mechanism that is able to drive the inner plunger by twisting a knob on the side of the device. This processing station was designed around a 60 mL syringe.
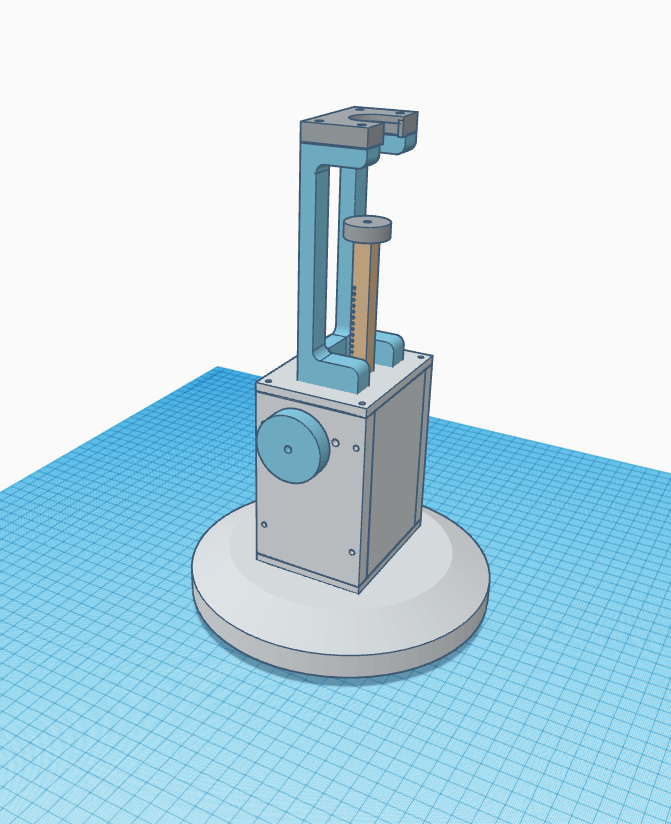
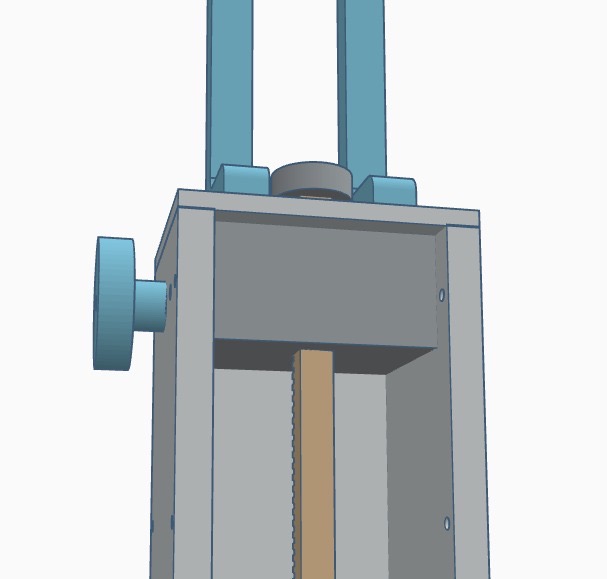
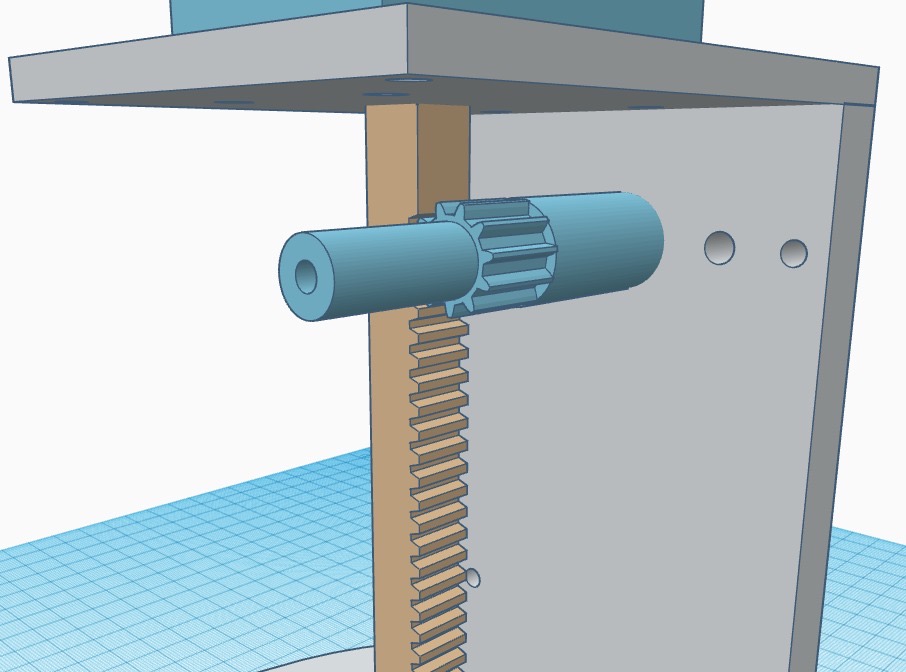
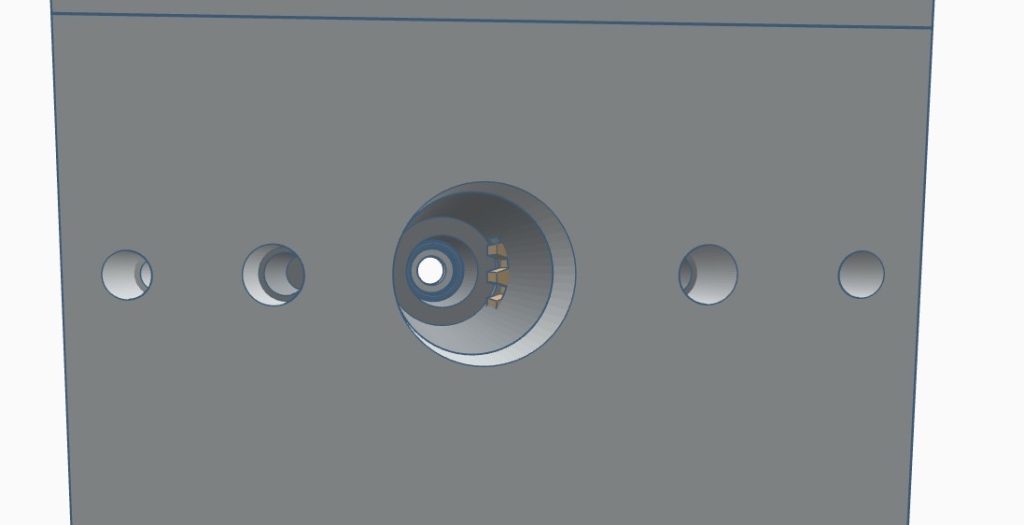
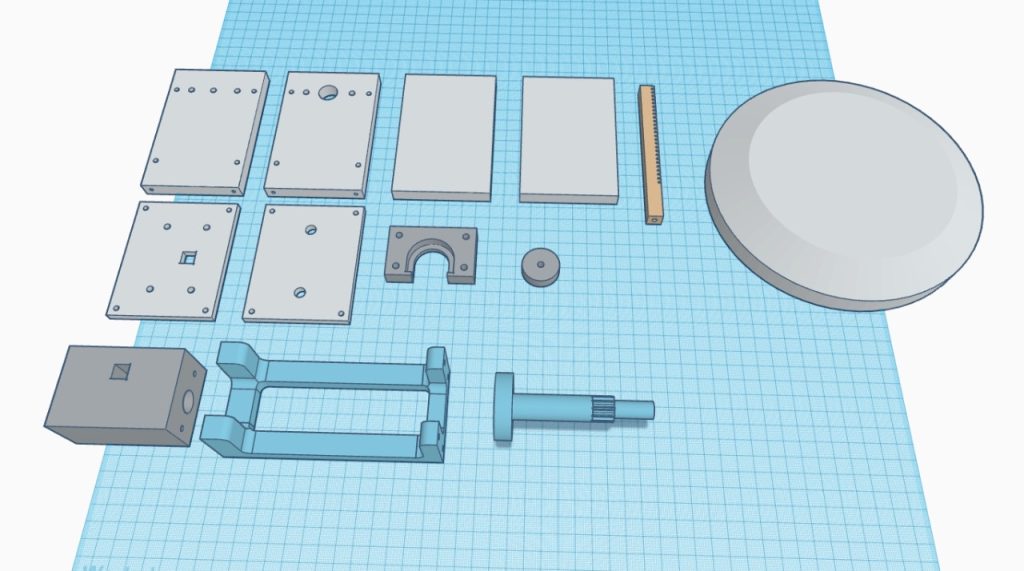
Purpose of the Processing Station
In order to make the DIY PRP system function as intended, the 60 mL syringes must be made to fit within the swinging buckets of the centrifuge by lightly modifying them. Two modifications are required:
- The syringe plunger must be cut off, leaving no material of the plunger extruding from the bottom of the barrel.
- The barrel flange must be cut down a couple millimeters to allow the syringe to slide down into the 50 mm bucket.
With these modifications completed, the syringe plungers and internal rubber stoppers can no longer be easily manipulated, hence the creation of the bench-top processing station which is used in the manipulation of the internal rubber stopper.
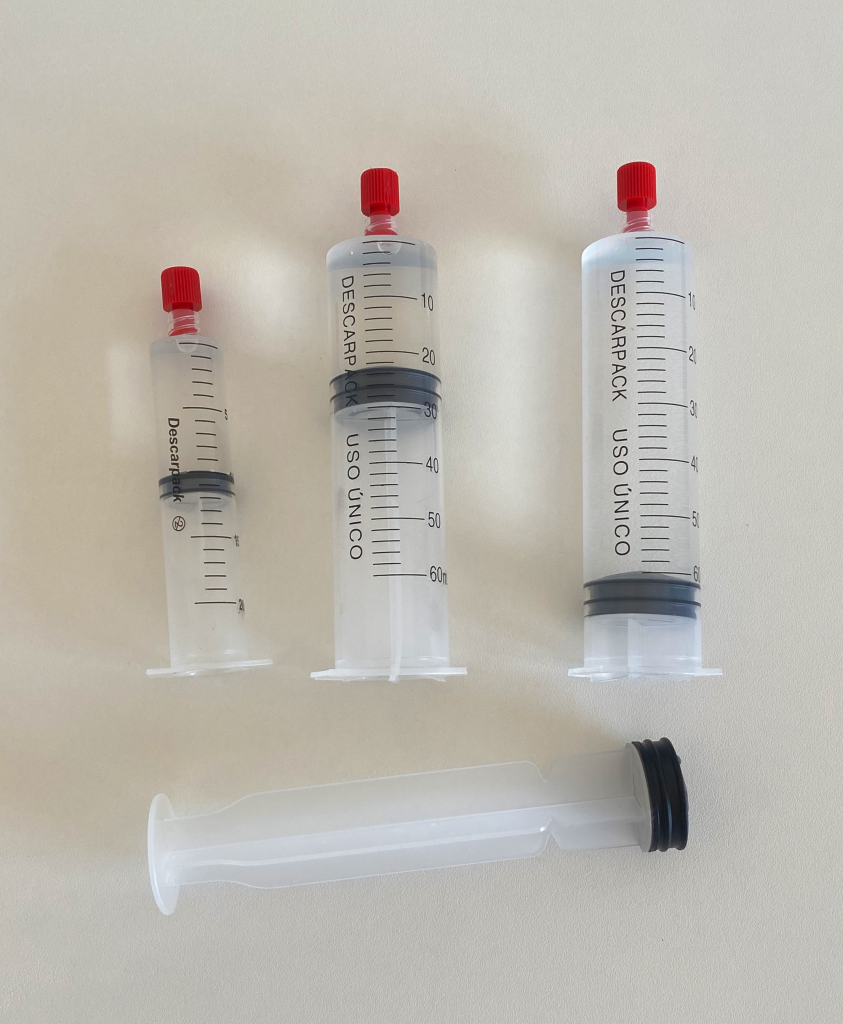
Design
This processing station designed using TinkerCAD, a free and accessible 3D design software. The CAD project is available on TinkerCAD for anyone interested in reproducing the design.
The material chosen for the production model was billet aluminium in 10 mm thickness, and a single block of at least 40 mm thickness. The overall cost of aluminium shouldn’t cost more than $50 USD. The base plate could be cut from steel, to weigh down the processing station on the bench top and save the cost of using aluminium. The processing station’s walls are meant to be 10 mm aluminium. Both laser cutting and CNC machining are required to fabricate this design.
This design does allow for the modification and introduction of a separate rack and pinion mechanism.
Design Criteria
- Cost-Effectiveness: The total cost of $500 is significantly lower than commercial alternatives which can be as much as $2,000.
- Ease of Construction: Utilizing aluminium in the fabrications reduces the difficulty of machining and finishing of the individual parts.
- Performance: Performance is determined by the tooth count and tooth size of the rack and pinion mechanism and isn’t a fixed measurement. The resolution of the movement can be increased by changing these measurements.
- Scalability: By using smaller plunger drive inserts, the manipulation of smaller syringes is theoretically possible.
Materials and Costs:
- Raw Aluminium Blocks: $50 USD
- Steel Base Plate: $20 USD
- Rack and Pinion: $50 USD
- Machining and Labor: $250 USD
- Anodization: $100 USD
- Various Hardware (screws, etc): $30 USD
- Total: $500 USD
By following this design, you can achieve a high resolution movement bench-top processing station, functional for the preparation of PRP at a fraction of the cost of commercially similar units, while ensuring precise control of the plunger’s movement.
Alternative Design Option
Constructing the processing station from billet aluminium carries a premium cost and may not be ideal for some people. A more economical option was designed that requires working with 15 mm composite MDF and some basic hand tools to modify some of the pieces. The design was made using TinkerCAD and the CAD project is available to download.
Plastic rack and pinion gear assembly kits are viable options for supplementing as the primary drive mechanism. The plastic gears must be epoxied to the metal axle shafts to remain stable and feasible.
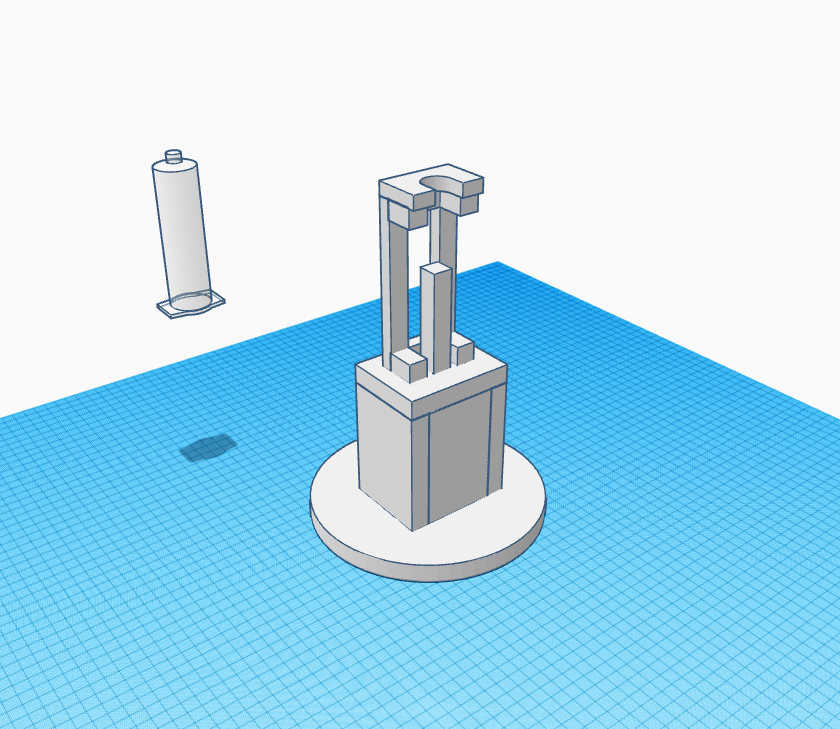
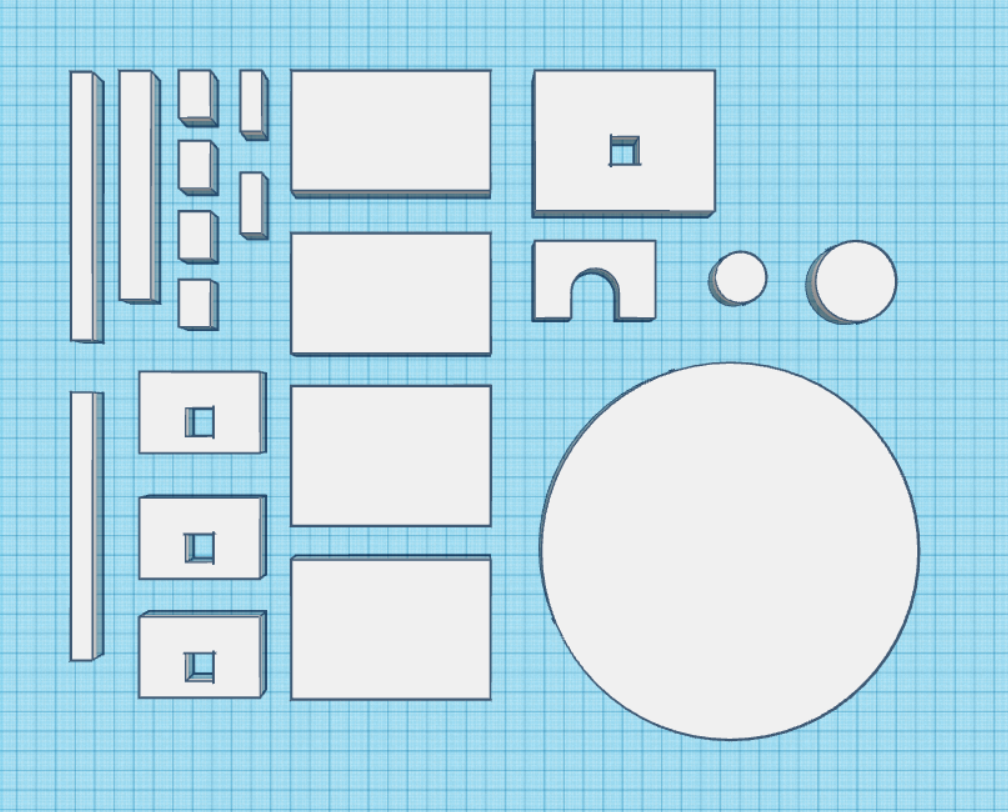
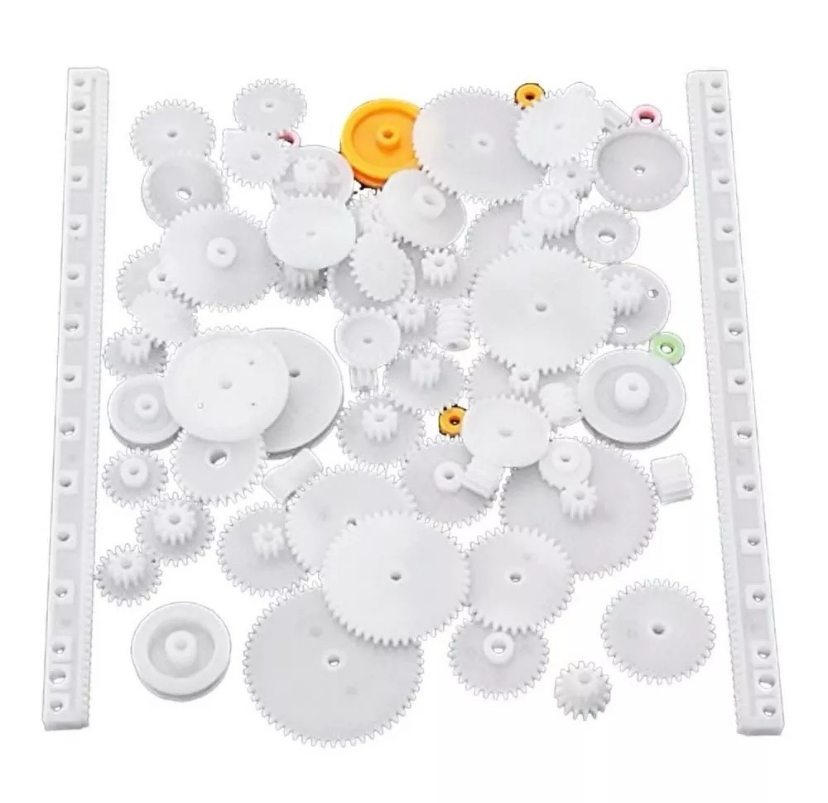
Proof-of-Concept Device
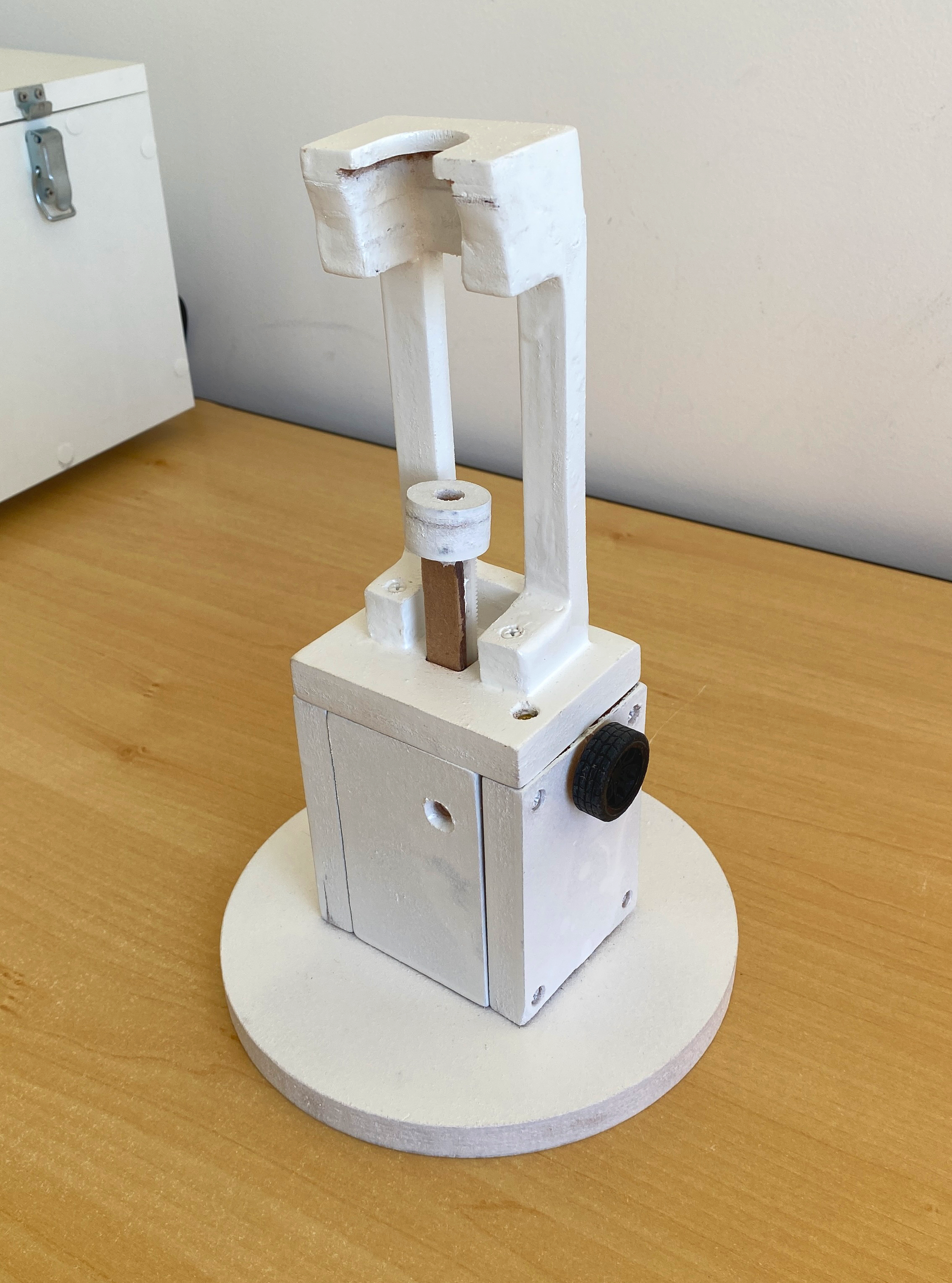
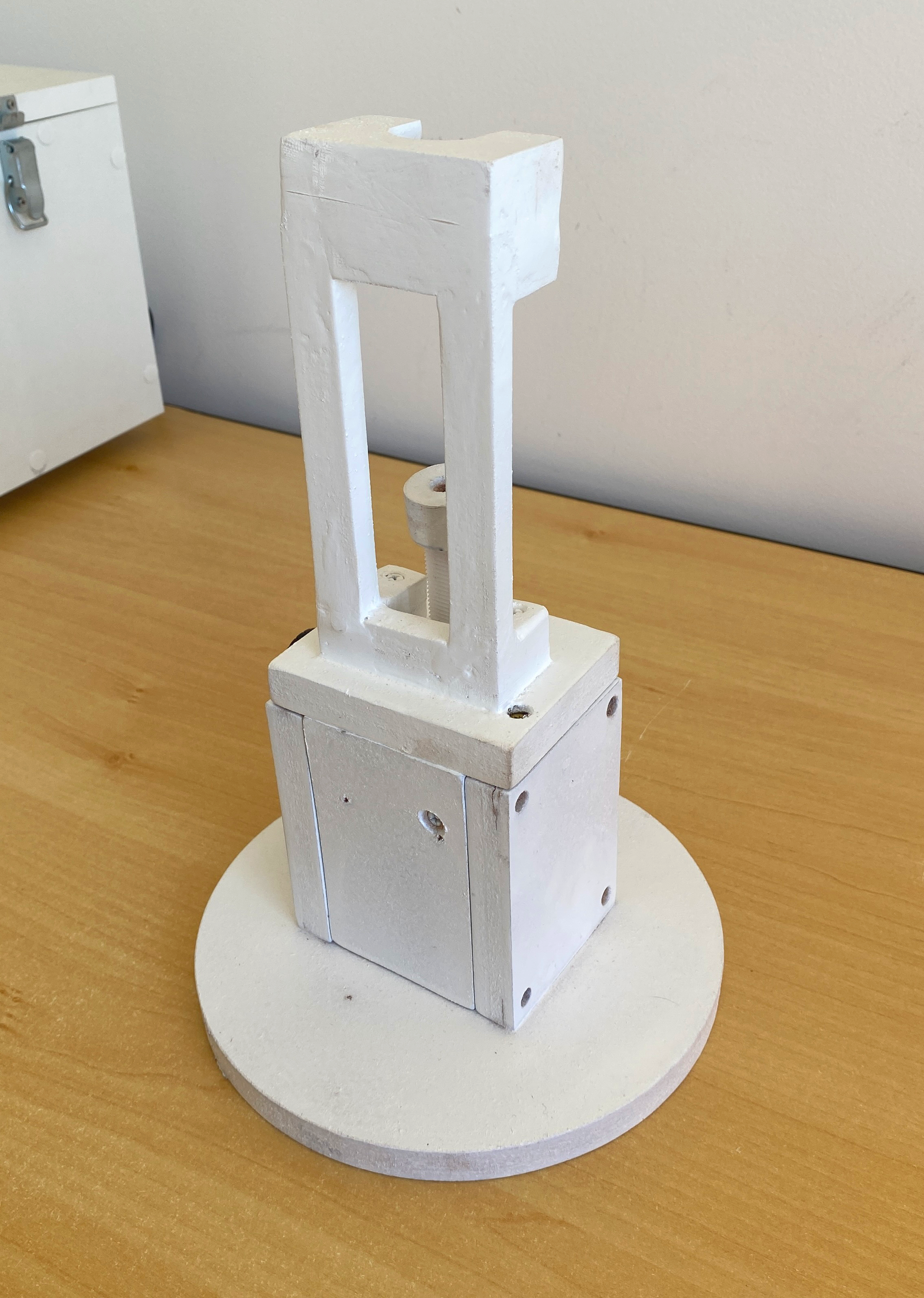
MDF Version (Proof-of-concept)
The MDF version of this processing station is a far more economical option and doesn’t require laser cutting or the machining of metal parts. The main downside is that the assembly process is difficult on this scale with 15 mm MDF and the final product may not present as clean of an aesthetic as desired, but in the context of home-use, the device more than suffices.
- Cost-Effectiveness: The total cost of $80 is significantly lower than aluminium alternative which is about $500.
- Ease of Construction: The use of MDF makes assembling this processing station possible at home with simple tools. A carpenter will need to prepare the individual block pieces, of course.
- Performance: The performance of the MDF version with the use of a plastic gear set is reasonably high, producing a high resolution rack and pinion drive movement, ensuring precise plunger manipulation.
- Scalability: By using smaller plunger drive inserts, the manipulation of smaller syringes is theoretically possible.
Materials and Costs:
- Pre-cut MDF Blocks: $40 USD
- Rack and Pinion Gear Kit: $20 USD
- Various Hardware (screws, etc): $20 USD
- Total: $80 USD
Construction of the MDF Processing Station
Remembering that this MDF version is indeed rough around the edges, yet every bit as functional as the aluminium prototype, at a fraction of the cost, proving the concept. This version takes advantage of inexpensive and readily available plastic rack and pinion gear assemblies that require little modification to work. The resolution of the movement is surprisingly precise and this option should be considered for home use.
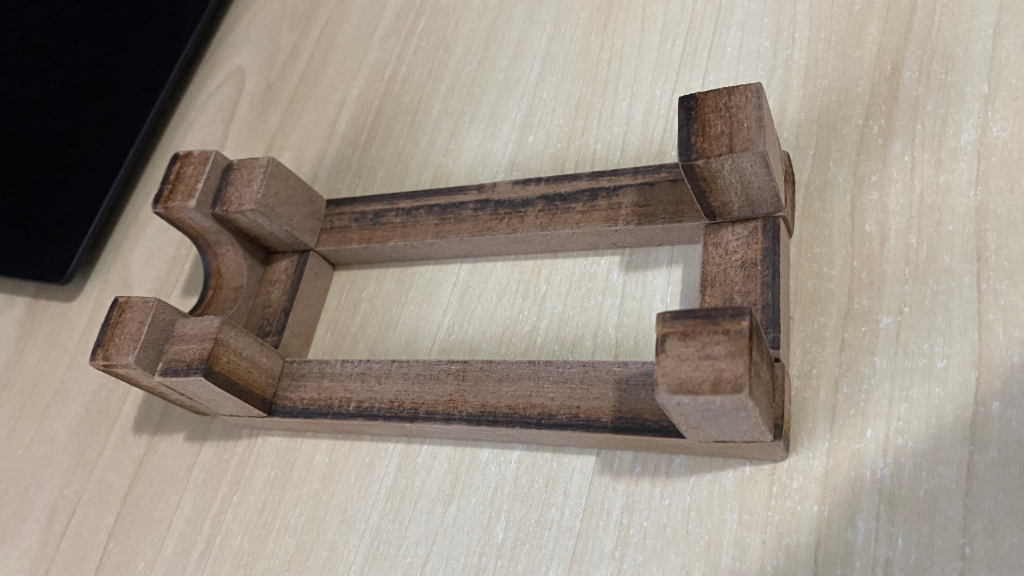

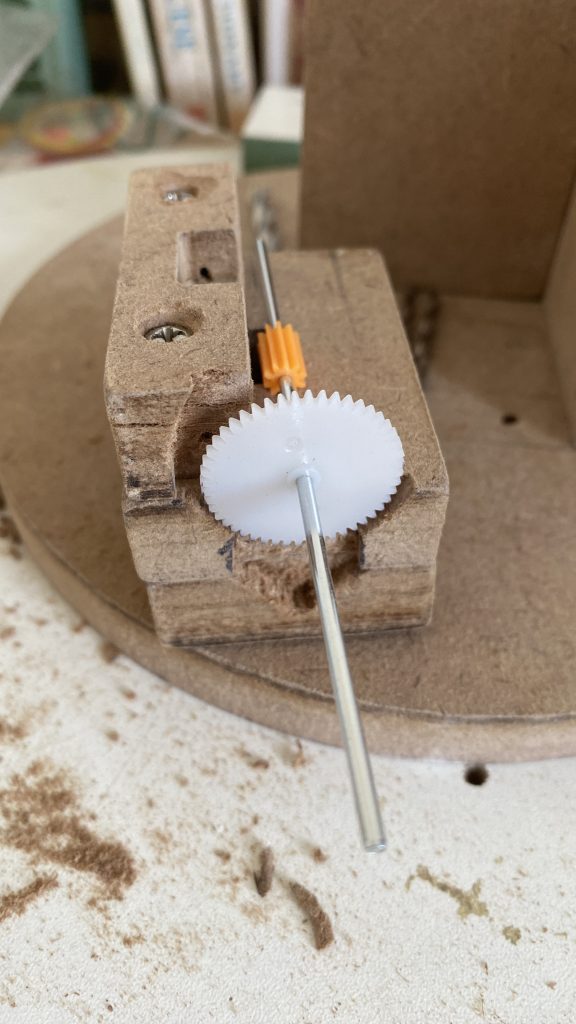
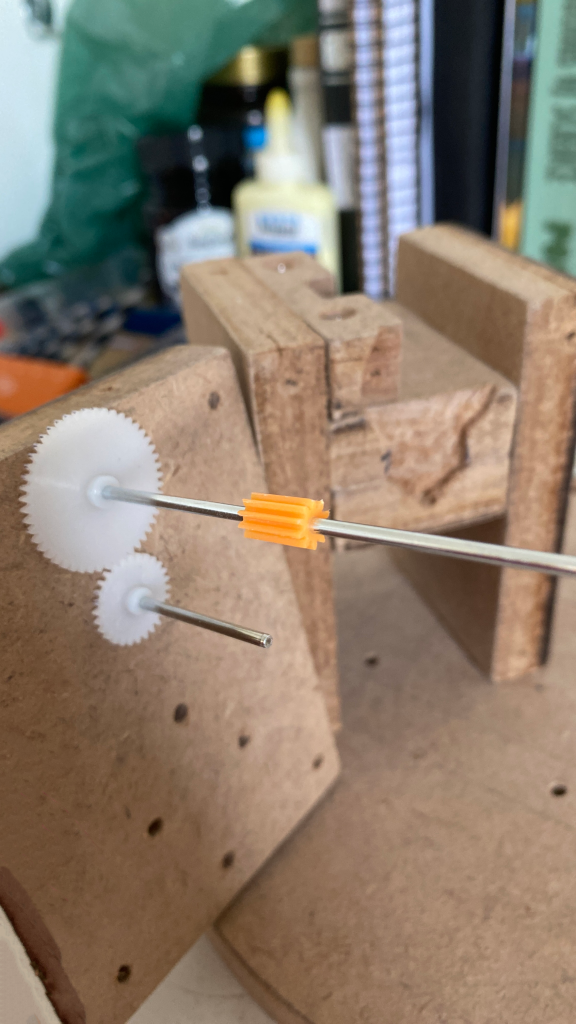
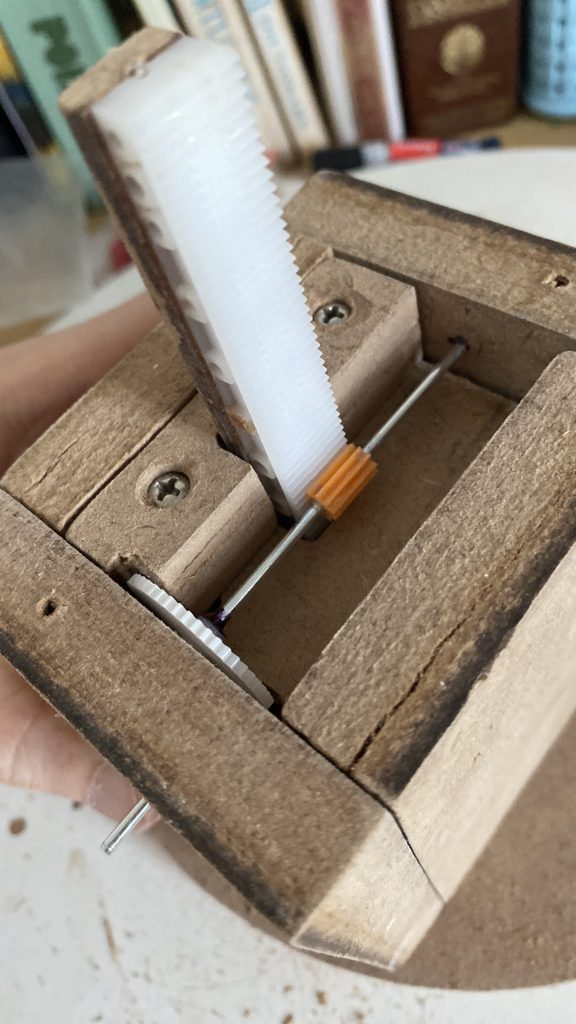
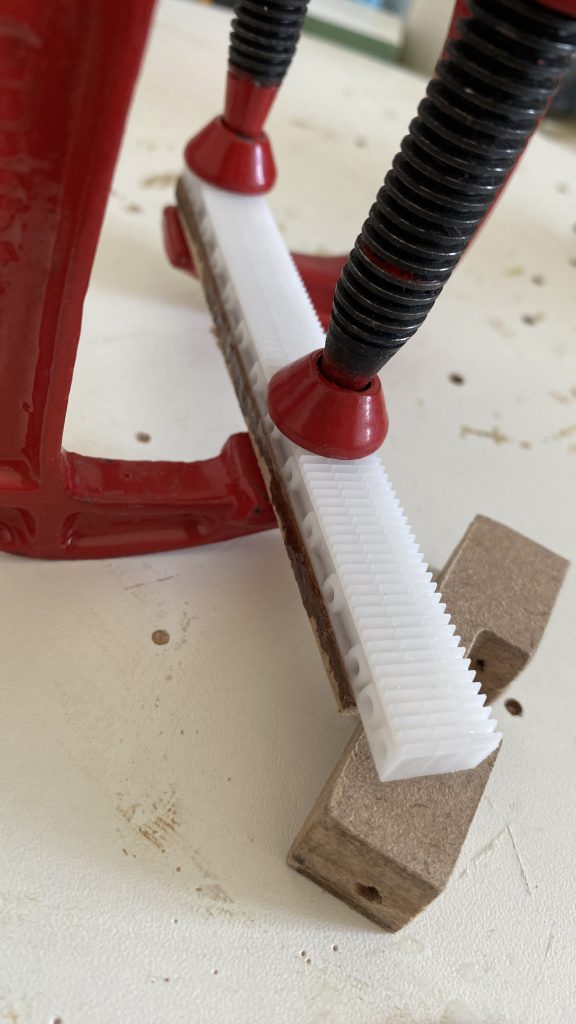
Operating Limits and Procedures
To effective operation, follow these procedures:
- Rack and Pinion Actuation: Actuating the rack and pinion should be done with careful, concise movements, ensuring not to over-torque the assembly or drive the assembly beyond the physical extension limits.
- Syringe Placement: While the dimensions of the processing station are designed to secure a 60 mL syringe, depending on the drive back characteristics of the rack and pinion system, the syringe could become loose against the top securing plate and may require constant positive tension on the rack and pinion operating knob.
By adhering to these procedures, you can maintain the integrity of your bench-top processing station and ensure efficient operations.
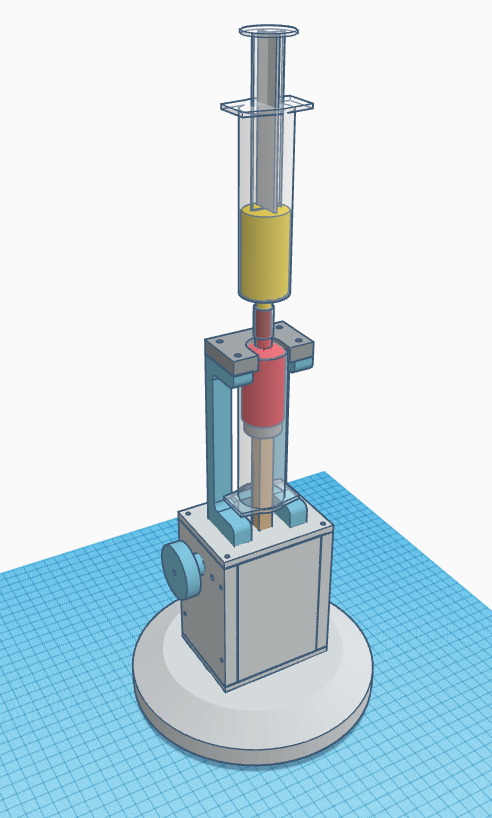
Leave a Reply